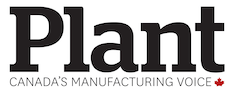
Lithion Technologies completes construction of commercial plant and signs agreements
By Plant Staff
Business Operations Economy Operations Sustainability Automotive Construction Energy Transportation battery manufacturing construction electric echicles emissions environment manufacturing marketingThe company is now in the commissioning phase to ensure its processes operate safely and effectively.

LITHION TECHNOLOGIES COMPLETES THE CONSTRUCTION OF ITS FIRST COMMERCIAL PLANT (CNW Group/Lithion Technologies)
MONTREAL — Lithion Technologies (Lithion), a company that develops, deploys, and operates patented technologies to recycle lithium-ion batteries and create a circular supply of their strategic materials, announces the completion of the construction of its first commercial critical mineral extraction plant, Lithion Saint-Bruno, located in St-Bruno-de-Montarville, near Montreal, in Canada.
Over the past several months, the team reportedly built a lithium-ion battery critical mineral extraction plant. Every piece of equipment has been installed, many of which were tailor-made to suit its unique technologies and processes. The company is now in the commissioning phase to ensure its processes operate safely and effectively. Lithion Saint-Bruno has a team of 20 Lithioneers, and at full capacity, the plant will employ 60 people.
During the plant construction, Lithion’s commercial activities progressed with the signing of multi-year battery feedstock agreements, and the receipt of several batteries. The first battery treatment steps, such as dismantling, have also started. These strategic agreements involve local partners as well as large Canadian, American, and international corporations, all part of the electric vehicle ecosystem.
To create the circularity of battery materials, Lithion has developed a two-step recycling process with an environmental impact significantly smaller than mining. The first step, performed at Lithion Saint-Bruno, is the extraction of the critical minerals concentrate, or black mass, from batteries and non-conforming products from their production. Black mass is made of lithium, nickel, cobalt, manganese, and graphite.
The second step is a hydrometallurgy process to separate and purify the black mass to produce strategic materials of the highest purity so they can be looped back into the production of new batteries.
“What an exciting achievement to have completed the construction of our first commercial plant”, expressed Benoit Couture, President and CEO of Lithion. “It’s a major milestone towards the realization of our dream of sustainably closing the loop of battery materials. And this is just the beginning. We will build more recycling plants, supplied by a network of battery collection and storage facilities, across Canada, the United States, and Europe to ensure the energy transition is a sustainable solution for the generations to come.”
“Today, we’re adding a new link to our integrated battery value chain. From mining to recovery, Québec stands out for producing the greenest battery in the world. The inauguration of the first commercial plant for Québec-based Lithion Technologies strengthens our industry and opens the door to a battery circular economy in Québec,” stated Pierre Fitzgibbon, Minister of Economy, Innovation and Energy, Minister Responsible for Regional Economic Development and Minister Responsible for the Metropolis and the Montréal Region.